전력의 송·배전과정에서 케이블 자체의 전기저항으로 전력 손실이 발생하는 구리 전력선과 달리, 영하 196℃ 이하의 극저온에서 전기저항이 제로(0)가 되는 초전도 현상을 이용한 제품으로 전력 손실이 매우 적고 대규모 전력 송·배전이 가능한 "꿈의 전력선" 입니다. LS전선은 2004년 덴마크, 미국, 일본에 이어 세계 4번째로 교류 제품 개발에 성공했으며, 2013년 세계 최초로 직류 제품을 개발하여, 교류와 직류 기술을 모두 보유한 세계 유일의 회사입니다.
공정 단계
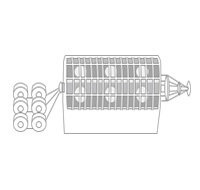
포머
신선에서 만들어진 지금 2~3mm 굵기의 신선재를 여러 가닥 모아서 새끼줄을 꼬는 것처럼 한 가닥을 여러 번 꼬아서 15~40mm의 굵기로 만듭니다.
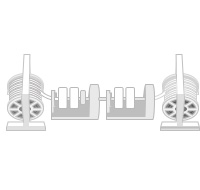
지권
초전도 케이블을 만드는 과정 중 가장 중요한 공정입니다. 전류를 통전하는 초전도 도체층 상부에 절연체인 PPLP를 권선하고 자기 차폐를 위한 초전도 차폐층을 권선해줍니다.
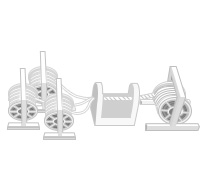
연합
앞의 과정에서 생산된 상 별 도체를 하나로 결속해주는 연합공정을 진행합니다.
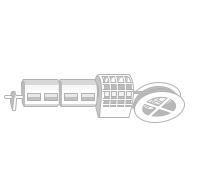
1차 금속시스
연합된 도체의 초전도성 유지를 위한 액체질소 순환용 질소조를 고온 압출 및 용접방법으로 알루미늄 혹은 스테인리스스틸과 같은 금속물질로 만들어줍니다.
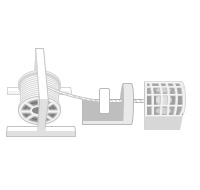
단열층(횡권)
질소조 상부에 외부 열전달을 차단하기 위한 MLI tape와 Thermal spacer를 차례로 만들어줍니다.
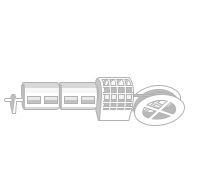
2차 금속시스
단열층부 상부에 외부 열전달 차단용 진공 상태 유지를 위해 진공조를 고온 압출 및 용접방법으로 알루미늄 혹은 스테인리스스틸과 같은 금속물질로 만들어줍니다.
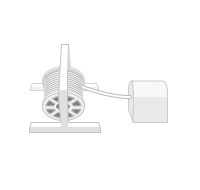
방식층
2차 금속시스 상부에 다시 한번 PVC 또는 PE를 입혀주는 과정으로 역시 고압으로 물질을 분사하고 고열로 한번 더 코팅해줍니다.
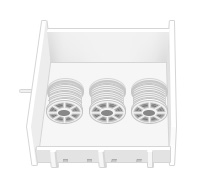
진공 및 건조
상위 공정의 건전성 평가를 위하여 70℃ ~ 80℃범위의 건조룸 투입과 동시에 진공배기를 실시합니다.
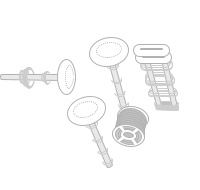
검사
엄격한 검사를 거쳐 제품을 출하 합니다.
초고압케이블은 220kV ~ 345kV급의 케이블로 발전소에서 만든 전력을 송전하는데 사용 됩니다. 송전시 케이블에 걸리는 높은 전압에 대해 강한 내구성을 지녀야 하며 대용량의 전력을 최소한의 손실로 보낼 수 있는 능력을 갖추어야 합니다. LS전선은 세계 최고 수준의 다양한 초고압 케이블을 고객들에게 제공하고 있습니다.
공정 단계
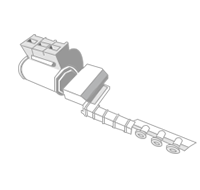
SCR(Southwire Continuous Rod System)
구리(Cu) 원소재를 용해로에 투입하고 녹인 다음 지름 8~9mm의 원형으로 뽑아냅니다.
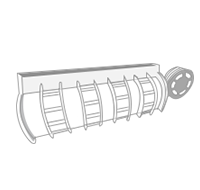
신선
SCR공정에서 만들어진 손가락 크기의 도체 가닥을 다시 가늘게 만듭니다.
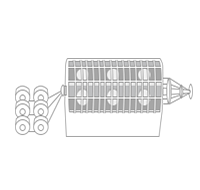
연선
신선에서 만들어진 신선재를 여러 가닥 모아서 새끼줄을 꼬는 것처럼 한 가닥을 여러 번 꼬아서 10~60mm의 굵기로 만듭니다.
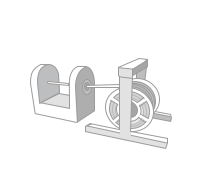
연합
연선과정에서 만들어진 도체를 하나로 결속해 주는 작업입니다.
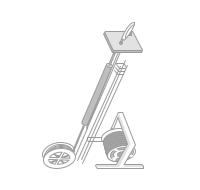
절연
XLPE 케이블을 만드는 과장 중 가장 중요한 과정입니다. 앞서 만든 도체에 흐르는 전기가 누설되니 않도록 하는 공정으로 도체 상부에 XLPE를 피복 압출하여 고온, 고압에서 가교 후 냉각하여 절연체를 만들어줍니다.
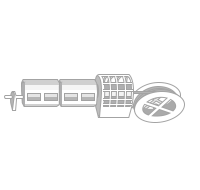
금속시스
앞의 과정에서 도체를 절연체로 감싼 후에 그 절연체를 보호하기 위하여 바깥쪽을 알루미늄 혹은 연(Pb)으로 덮어줍니다. 높은 압력과 열을 이용하여 덮어줍니다.
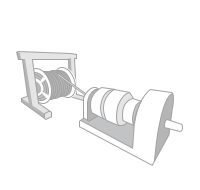
방식층
앞서 금속으로 한번 포장한 것을 다시 한 번 PVC 또는 PE을 입혀주는 과정으로 고열, 고압으로 자재을 압출하여 코팅해줍니다.
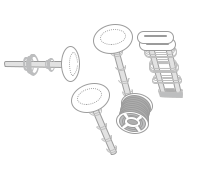
검사
초고압 전선의 경우 불량 발생 시 엄청난 위험을 초래하므로 엄격한 검사를 거쳐 출하됩니다.
광통신은 전기 신호를 광(光) 신호로 바꾸어 유리섬유를 통하여 전달합니다. 다른 통신 케이블에 비해 대역폭이 넓어 데이터 전송률이 뛰어나고, 크기와 무게가 작아 전선의 크기를 줄일 수 있으며, 광 형태로 전송되어 자기장이나 전기적인 간섭에 강합니다.
공정 단계
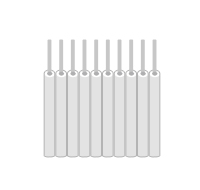
모재
코어와 클래딩으로 구성된 유리봉 형태의 광섬유 원재료
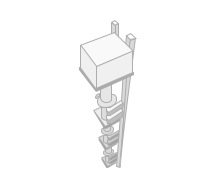
인선 공정
2차 모재를 용해로에서 연화시키면서 125㎛의 굵기의 가느다란 유리섬유로 뽑아내는 과정입니다. 뽑아낸 섬유는 외부의 수분 또는 충격으로부터 보호하기 위하여 245㎛로 레진을 입혀 코팅한 후 경화시킵니다.
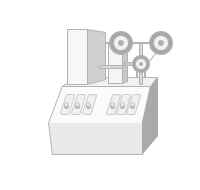
강도시험 (Proof Test) 공정
광섬유에 인장력을 가하여 기계적인 인장강도를 시험함으로써 광섬유의 장기적인 수명을 보장하기 위한 공정입니다.
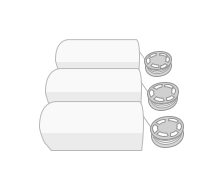
인쇄 공정
앞서 생산된 광섬유들을 식별하기 위해 12색 체계로 코팅시키는 공정입니다.
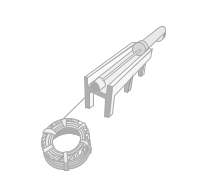
튜빙 공정
광케이블의 기본 유니트를 만드는 공정으로써, 코팅된 광섬유를 PBT 또는 PP 재질로 된 튜브 내에 여러 가닥을 삽입하는 공정입니다.
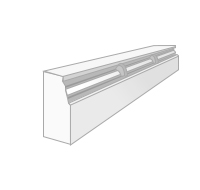
집합 공정
케이블 코어를 형성하기 위해 중심 인장선 주위에 튜브 유니트를 집합하는 공정으로 기본 유니트들을 여러 가닥 꼬아서 집합 유니트를 형성합니다. 광케이블 사용 시 편리한 작업성을 위해 SZ방향으로 튜브가 꼬여져 있습니다.
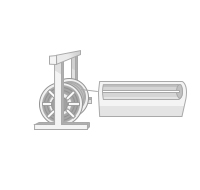
시스 공정
집합된 케이블의 심(core) 주위로 폴리에틸렌(PE) 또는 무독성 난연 폴리에틸렌(PE) 등을 압출하여 집합 유니트를 충격으로부터 보호할 수 있는 외피를 만드는 공정입니다. 고객의 다양한 요구에 따라 Steel Tape 외장 등의 다양한 구조로 제작됩니다.
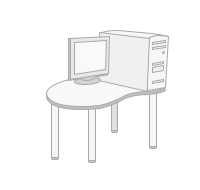
검사
고객의 요구사항에 맞추어 검사가 엄격히 진행됩니다. 광학특성으로는 PMD, MFD, 차단파장 등이 있으며, 기계환경 특성으로 비틀림, 방수, 온도시험, 충격, 압축 등의 테스트를 진행합니다.